Jeffrey E. Stines
Director of Marketing, American Ultraviolet
The first documented application of UV for the purpose of disinfection was a 1910 prototype drinking water plant in Marseille, France1. Since that time, effective use of ultraviolet energy for reduction of microorganisms has spread to a wide variety of applications including drinking and wastewater, indoor air quality, food safety, horticulture, healthcare and consumer products. The list of current applications is far too long to fully list here, so the simplest summation is that UV-C technology is now widely used to effect reduction of bacteria, viruses, molds and other microorganisms in air and liquids and on surfaces.
So, what is UVGI?
Ultraviolet (UV) energy is a portion of the electromagnetic spectrum. The electromagnetic spectrum is the range of all types of known electromagnetic energy – also known as electromagnetic radiation. The term radiation simply means energy that travels and spreads out as it travels2.
There are seven types of radiation in the electromagnetic spectrum:
- Radio
- Microwave
- Infrared
- Visible
- Ultraviolet
- X-ray
- Gamma
The ultraviolet portion of the electromagnetic spectrum is right between x-ray and visible light, containing wavelengths from 10 to 400 nm. Since human vision cannot perceive wavelengths below 400nm, ultraviolet "light" is invisible to the human eye.
Further subdivision of ultraviolet radiation leaves us with four generally accepted bands of UV:
- VU-V: 10-200 nm (vacuum UV)
- UV-C: 200-280 nm
- UV-B: 280-315 nm
- UV-A: 315-400 nm
The sun emits the full UV spectrum as approximately 10% of sunlight. The shorter wavelengths (VU-V, UV-C, and most of UV-B) are strongly attenuated by the earth's ozone layer and no measurable VU-V or UV-C from the sun reaches the earth's surface.
How does UVGI work?
UV-C wavelengths (200 to 280 nm) are readily absorbed by the DNA and RNA of microorganisms. When absorbed, UVGI damages the structure of the DNA by forming thymine dimers, which prevent the microorganism from replicating. In simpler terms, microorganisms replicate by copying their DNA, and UVGI damage to the DNA makes it so the microorganism can no longer replicate, nor perform vital cellular functions. The magnitude of reduction of microorganisms is directly related to their resistance to UVGI and the quantity of UVGI energy delivered.
UV-B wavelengths (280 to 315 nm) have also been shown to have a germicidal effect on nucleic acids (DNA and RNA), just to a lesser extent than the UV-C wavelengths from 200 to 280 nm. The collective UV-C and UV-B spectrum (200 to 315 nm) is considered actinic, meaning these wavelengths produce a photochemical reaction.
How are UV-C and UV-B wavelengths created on the earth's surface?
As it turns out, human beings are rather clever and have discovered several methods of emitting all or some of the UV-C spectrum without the need to circumvent the ozone layer. Low-pressure mercury vapor (LPMV) lamps, medium-pressure mercury vapor (MPMV) lamps, pulsed xenon lamps, excimer lasers, light emitting diodes (LEDs) are all currently being used as UV-C sources. Excimer lasers are mostly used for research, medical applications and electronics manufacturing and will not be discussed further in this article.
Germicidal UV sources
Table 1. Typical commercial germicidal UV sources
Low-pressure mercury vapor
Low-pressure mercury vapor germicidal lamps are the most prolific UV sources used across all applications. They emit energy at two distinct peaks – 185 nm and 253.7 nm – and have been commercially available since the mid-20th century.
LPMV lamps available in a wide variety of configurations, but share the following characteristics:
- The envelope of the lamp is made from glass (either quartz or soft).
- The lamp is filled with argon gas, an argon/neon mix or special rare gas mix.
- A small amount of mercury (liquid or solid) is inside the lamp. Depending on the type of LPMV lamp, this ranges from <10 mg up to 100 mg.
- A filament or electrodes is present inside the lamp envelope.
- The base of the lamp (or a base at both ends) brings incoming current from the power source to the electrodes or filaments inside the lamp.
The operation of a LPMV lamp is as follows:
- Power is brought to a ballast.
- The ballast converts the incoming power to the designed power input required by the lamp.
- Current passes between the electrodes (or through the filament) and through the gas (or gas mixture) inside the lamp.
- The current passing through the environment inside the lamp vaporizes the mercury inside the lamp at a low pressure.
- The vaporized mercury at low pressure radiates mainly the 185 nm and 253.7 nm spectrums.
- Depending on the type of glass envelope used, the lamp either emits only 253.7 nm or emits both 253.7 nm and 185 nm wavelengths.
- The 253.7 nm wavelength is within the UV-C spectrum and will create the dimers that inactivate the DNA or microorganisms.
- The 185 nm wavelength on its own has no germicidal effect until it interacts with an oxygen-containing environment, at which point it will create O3 (ozone). Ozone is effective in enhancing germicidal efficacy but also presents a potential health hazard to humans.
Types of LPMV UV Lamps
- Standard Output (425 mA)
- High Output (600 to 800 mA)
- Amalgam (1 to 10 A)
All three of the above are considered LPMV lamps. A standard output LPMV lamp is driven at 425 milliamps (mA). A 33″ standard output LPMV lamp will typically have a rated output of 120 µW/cm², measured at a distance of one meter. A standard output lamp's output in the real world is dependent on ambient temperature around the lamp. Forty degrees Celsius is the maximum ambient temperature for a standard output LPMV lamp. Above that, lamp output will drop considerably below 90% of its rated output. When driven by an appropriate ballast, standard output lamps function within design parameters in still air.
High output lamps are driven at 600 to 800 mA and use more substantial electrodes. High output lamps can emit approximately twice the intensity of their standard output counterparts, and high output lamps have a slightly wider range of acceptable ambient operating temperatures without compromising output intensity. However, proper cooling of high output LPMV lamps is required in still air as the lamps will, in still air, warm up to the point where they exceed their maximum ideal operating temperature. High output LPMV lamps work quite well in HVAC applications where air is typically blowing across the lamp surface and keeping ambient temperature around the lamp below 40°C.
Amalgam lamps are driven at one to 10 A and have indium added to the mercury inside the lamp envelope. They offer the widest range of ambient operating temperature with consistent output across the range and can produce up to six times the output intensity of their standard output counterparts.
Medium pressure mercury vapor
Medium pressure mercury vapor (MPMV) lamps operate in much the same way as low-pressure mercury vapor lamps, but the pressure inside the lamp envelope is greater, which broadens the potential spectral output of the lamp to a typical range of 200 to 600nm. The spectral output of MPMV lamps can be narrowed and shifted within that range (as well as to produce 185 nm and, therefore, ozone) by the type of glass envelope used in construction of the lamp and by metal additives (such as iron and gallium) inside the lamp.
MPMV lamps offer significantly higher UV-C (and overall energy) output than LPMV lamps; however, they also operate at much higher temperatures and a smaller percentage of their output is in the UV-C spectrum, so they are technically less efficient in terms of energy input to UV-C energy output than LPMV lamps. Additionally, MPMV lamps contain higher quantities of mercury than LPMV lamps, and EPA guidelines regarding hazardous waste must be consulted in disposal of these lamps. MPMV germicidal lamps are typically used in high flow water treatment applications requiring large amounts of UV-C radiation in a very short period.
Pulsed xenon
Pulsed xenon (PUV) lamps are also known as flashtubes or flashlamps. These are typically constructed from a quartz tube filled with xenon gas. Rather than constantly emitting germicidal UV energy like a UV lamp, pulsed xenon lamps emit multiple, brief, high-power pulses of broad spectrum (200 to 1,100 nm) energy. PUV lamps' pulse rate and duration of pulse vary in design, but many pulse as much as 120 times per second.
Germicidal effects are equivalent to continuous UV disinfection sources when the same total amount of UV energy (fluence) is delivered to the target3. PUV lamp systems for disinfection are commercially available and have seen considerable adoption over the last decade due to successful real-world case studies in healthcare settings. PUV lamps operate at high temperatures and high bulb pressures, so safety issues related to this need to be considered in design and application of these systems.
UV-C LEDs
Ultraviolet light emitting diodes are much like the LEDs used in visible light applications (such as televisions and indoor lighting) and differ from these primarily in the wavelength of energy emitted. LEDs are monochromatic, meaning they emit one specific wavelength, so an ideal germicidal UV LED would emit the 265 nm wavelength at the peak of germicidal efficacy curve, enabling them to achieve equal reductions in microorganisms to mercury vapor lamps with lower levels of UV energy due to the 265 nm wavelength being the most lethal wavelength to nucleic acid.
UV-C LEDs are in existence at this time and have been successfully used in laboratory settings to demonstrate efficacy in microbial reduction. As of the writing of this article, LEDs in the UV-C spectrum are still improving in output and useful lifetime, so applications in commercially available products are limited to smaller, lower powered equipment at this time. The long-term implications of UV-C LEDs are quite promising due to their highly configurable nature, compact size, germicidal efficacy at 265 nm and the absence of mercury in the technology.
Glossary of UV-C terminology
Intensity/irradiance
Intensity (or irradiance) refers to the power of the UV source (i.e., how much light is being delivered per second). This is typically expressed in terms of wattage per unit of area (such a microwatts per square centimeter or mW/cm2). Intensity at the target depends on the intensity of the UVGI source and the distance between the source and target. Simply put, intensity decreases as distance increases.
Fluence/dose
Germicidal energy delivered to the target. Fluence is the academically correct term, but the common vernacular still includes widespread use of both dose and dosage. The difference is that fluence refers to the amount delivered to the surface of the microorganism, whereas dosage implies the absorption of the energy delivered to the microorganism. In scientific terms, when measuring the amount of UVGI a system is delivering to the target, fluence is the correct terminology as different microorganisms will have varying UVGI absorption rates. It can be said it is delivering a specific total amount of energy to the target, but the actual dosage received by two different microorganisms will depend on their resistance to UVGI.
Fluence is a product of intensity and time and is typically expressed as joules per square meter (J/m2) or millijoules per square centimeter (mJ/cm2). A joule (J) equals a watt-second (W-s), so a fluence of one J/m2 is the same as one W-s/m2. The use of joules in the indication of fluence is useful in avoiding a common issue in casual discussions where intensity and fluence are often confused due to using similar sounding measurement units (i.e. W/m2 and W-s/m2).
Log reduction
To properly measure the effects of UVGI, use log reductions to quantify the results. In the most straightforward terms, log reduction works per the following chart:
Log reduction | Percent reduction |
1-log | 90% |
2-log | 99% |
3-log | 99.9% |
4-log | 99.99% |
Since margins of error of any magnitude exist with all measurement techniques, a 100% reduction isn't possible from a scientific perspective, so the current convention is to speak in terms of log reduction to more factually represent what can be empirically demonstrated.
Terminology varies in use and definition based on the regulatory agency presiding over a given industry segment. It's generally best practice to speak in the most specific and accurate terms possible when defining the parameters of UVGI applications. For example, instead of saying the goal is to kill MRSA with UV, a more appropriate and achievable goal would be to achieve a 3-log or greater reduction of MRSA by delivering an appropriate fluence of germicidal UV energy.
Before making any statements regarding sterilization, cleaning or disinfection, it is important to understand the specific definition of these terms in the context of the proper regulatory body for the application.
Viruses, molds, bacteria, etc.
Microorganism has come to be used as a convenient catch-all for the various "bugs" of interest in UVGI disinfection. It is more convenient to use than listing out viruses, molds, bacteria, yeasts, etc.
A useful distinction is between spore-forming and non-spore-forming microorganisms as the former are more resistant to UVGI and generally require a higher fluence for equivalent reductions to the latter. For example, Bacillus and Clostridium species of bacteria are spore-forming, whereas Staphylococcus is non-spore forming. So, by extension, a 3-log reduction of C.diff (Clostridium difficile) will require a greater fluence of UVGI than 3-log reduction of MRSA (Methicillin-resistant Staphylococcus aureus).
Many resources exist for fluence required for specific microorganisms and specific reduction levels and these resources are continually updated as new research is completed. Since this is a living, continually evolving reference, consulting the latest version of the UVGI inactivation database is the best course of action.
Wavelengths
Wavelength is how the various types of radiation within the electromagnetic spectrum are differentiated. Gamma radiation has the shortest wavelength and radio radiation has the longest wavelength. Ultraviolet radiation has shorter wavelengths than visible light and longer wavelengths than X-ray. For the purposes of this article in discussing UVGI, wavelength is measured in nanometers (nm).
Peak germicidal inactivation is historically shown at 265 nm, although there is currently some debate on this; 260 nm and 250 nm are also potential target wavelengths for optimal germicidal inactivation.
UV-C LEDs ideally will emit 265 nm energy, or whichever wavelength is ultimately found most effective, for optimal germicidal effect.
Lamp/bulb/emitter/fixture/device
In the context of UVGI equipment, these terms tend to have very loose definitions and are frequently used interchangeably in casual conversation. It is common for the terms lamp, bulb and emitter to all refer specifically to the UV-emitting lamp itself (exclusive of the rest of the fixture). It is also common for the terms emitter, fixture and device to all be used to refer to the complete UVGI assembly, including the UV lamp. It is always best practice to clarify exactly what portion of a piece of UVGI equipment is being discussed when any opportunity for ambiguity exists.
In this article, the term UV lamp means the UV-emitting component of the UVGI system for LPMV and MPMV systems.
Measuring UV irradiance and fluence
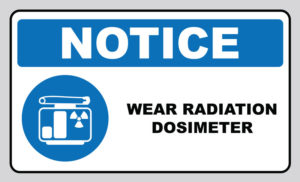
UVGI sources all share a limited lifespan (some longer than others), so measuring system performance over time is a critical component of successful implementation. To properly measure the intensity and fluence of a UVGI system, there are two main accessible methods: radiometers and dosimeters.
A radiometer will measure the intensity (and fluence in certain models) of a specified spectrum of electromagnetic radiation. For UVGI applications, the primary concern is typically in the UV-C section of the spectrum (200 to 280nm). The radiometer will consist of a sensor to pick up energy in the desired measurement spectrum and a meter to display the input to the sensor (or output that information to an external component of a monitoring system). Radiometers can be relative and display intensity as a percentage of the initial measurement of the system when new (or when last calibrated to 100%), or they can be absolute and display intensity in real time in a standard unit of measurement, such as W/m2. Some radiometers have the capacity to measure fluence, which is useful in applications with moving components.
A dosimeter is a photoreactive ink that is formulated to respond to a specific portion of the electromagnetic spectrum. In UVGI applications this would typically be the UV-C band. The dosimeter is a single use card or sticker that will change color to indicate fluence. It is positioned wherever a measurement of fluence is desired. A good dosimeter will not react outside the desired wavelengths it is designed to measure.
Radiometers are useful for real-time online monitoring of UVGI system performance in critical applications and dosimeters are useful for periodically evaluating system performance. Dosimeters are relatively inexpensive ($3 to $10/piece) single-use tools and radiometers can be somewhere between a tool and a scientific instrument and cost anywhere from a few hundred dollars to several thousand dollars. The logistics of the UVGI application should dictate which of these is most appropriate.
UV safety
Despite the multitude of positive outcomes of using UVGI for disinfection or air, liquids and surfaces, there do exists several safety hazards to humans that must be addressed. With proper understanding of the potential hazards and proper implementation of safety protocols, it is very easy to safely and effectively use UVGI technology without negative repercussions.
Broken glass
Except for LEDs, all UVGI sources use a quartz glass-type lamp envelope, which presents the potential hazard of broken glass. Depending on the application, lamps can be physically protected by the very enclosures that prevent eye and skin exposure to UV energy. In other instances, a UV-transmissive sleeve can be applied to the lamps, so all glass and mercury are contained within the sleeve in the event of a breakage. This is a very common solution in food and beverage manufacturing.
Mercury
LPMV and MPMV lamps contain mercury to emit the desired wavelengths of germicidal UV energy. In normal use this poses no hazard, but it does create issues in the event of broken lamps and disposal.
For broken lamps, the encapsulating sleeves mentioned in the above section on broken glass will contain the mercury. If the lamps are not encapsulated and mercury from the lamps requires cleanup, proper precautions for handling mercury must be taken and it should not be touched with bare skin under any circumstances.
For disposal, consult local ordinances and laws regarding disposal of mercury-containing devices. Most LPMV lamps' mercury content is like fluorescent lamps of similar size, so the same disposal guidelines apply. Many manufacturers offer low mercury LPMV lamps which use significantly less mercury than traditional LPMV lamps, lessening the environmental impact of disposing of spent lamps. MPMV lamps contain more mercury and do require special disposal. PUV xenon lamps and LEDs contain no mercury, so this does not apply to these types of UV sources.
Eye exposure
Actinic UV (200 to 315 nm) exposure of the eyes will cause a very painful sensation roughly four to 12 hours after the exposure occurs. The condition is known as keratoconjunctivitis and is also known as welder's flash and snow-blindness. While it can be extremely painful, it is a temporary condition that resolves within 48 hours. Actinic UV exposure causes inflammation of the cornea and conjunctiva, which causes the vision impairment and acute pain. Depending on the intensity and fluence of the source a photokeratoconjunctivitis can arise after even just a few minutes of unprotected exposure. There is no evidence to show any permanent damage in humans from this exposure, but it is extremely painful and should absolutely be avoided at all costs. In the event of eye exposure to actinic UV, the best course of action is to seek medical attention. Typically, a medical professional will provide a course of pain management for 48 hours.
UVGI systems should incorporate safety features to prevent accidental eye exposure. This may include optical shielding of the UVGI portion of systems operated in proximity to humans, safety interlock limit switches at access panels to UVGI sections of equipment and motion sensor shut offs for systems operated where personnel may accidentally enter the field of actinic UV energy.
If personnel must be in proximity to unshielded actinic UV, proper personal protective equipment (PPE) must be worn. Most safety glasses and face shields do not transmit UV at these wavelengths, but it is always better to ask than assume in the case of safety. Always ensure protective eyewear intended to be used near actinic UV sources is rated to block 200 to 315 nm energy.
Skin exposure
Actinic UV exposure of the skin will cause reddening of the exposed skin that will feel similar to sunburn. UV-C wavelengths are non-penetrative and will cause a strong reaction on the surface of the skin but lack the ability to deeply penetrate. UV-B wavelengths are those known to be carcinogenic in humans. No known data shows a carcinogenic effect in humans from UV-C exposure. Regardless, great care should be taken to avoid exposing bare skin to actinic UV of any wavelength. The same safety precautions for eye exposure by UVGI systems apply to skin exposure. As far as PPE, most regular clothing is enough to attenuate incidental UV exposure. Anyone working in an environment where direct actinic UV energy is present for any length of time must cover all exposed skin.
Exposure limits
Currently, "there are no OSHA-mandated employee exposure limits to ultraviolet radiation4". For exposure limits, the American Conference of Governmental Industrial Hygienists (ACGIH) publishes threshold limit values (TLVs®) and the values for UVGI are both source and wavelength dependent. The ACGIH's annual publication of Threshold Limit Values for Chemical Substances and Physical Agents & Biological Exposure Indices should be consulted in situations where UVGI exposure of personnel is unavoidable5.
Closing remarks
In summary, it's important to understand that while the various types of UVGI sources have their advantages and disadvantages across various applications, there is no one best source for every application. It's crucial to evaluate the source type used in an application in the context of that specific application and the requirements of the UVGI system as defined by the scope of the project. Much like a craftsman's toolbox, there are times when a hammer and nails are the best possible tool, but a hammer and nails aren't a great solution if the goal is to cut a board to a specific length.
As the UV industry continues to grow and mature, the continued cooperation and collaboration of research scientists, manufacturers of components, system manufacturers and regulatory agencies will be a great asset to the collective goal of advancing the proper, effective and environmentally conscious use of ultraviolet technology for the greater good of the world and all its inhabitants.
References
- "Ultraviolet light disinfection in the use of individual water purification devices"(PDF). U.S. Army Public Health Command. Retrieved 2014-01-08.
- https://imagine.gsfc.nasa.gov/science/toolbox/emspectrum1.html
- Kowalski, W. (2009) Ultraviolet Germicidal Irradiation Handbook: UVGI for Air and Surface Disinfection. New York, NY: Springer.
- https://www.osha.gov/laws-regs/standardinterpretations/2003-02-26
- ACGIH®. 2019 TLVs® and BEIs® Based on the Documentation of the Threshold Limit Values for Chemical Substances and Physical Agents & Biological Exposure Indices. ACGIH®, Cincinnati, OH (2019).